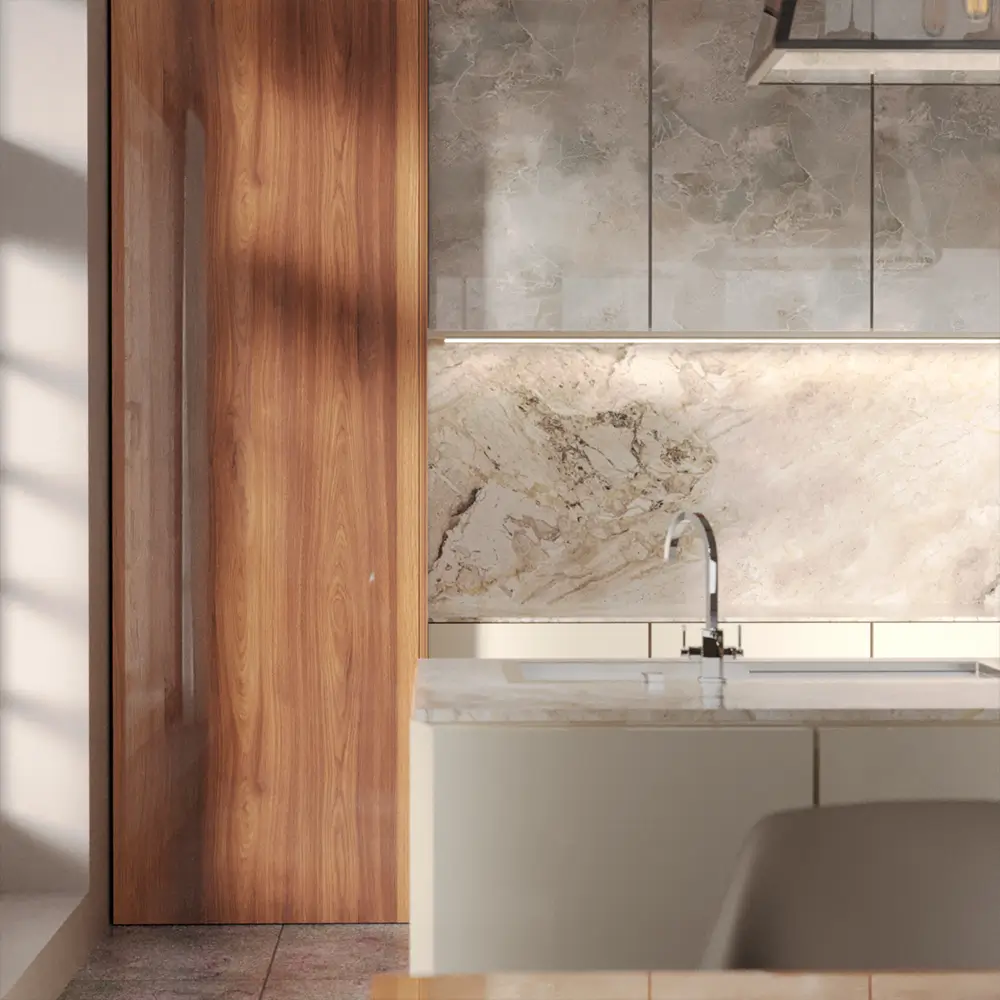
What is Particle Board?
Did you know that the word Sunta is actually a brand name for the particle board product? The word "Sunta", which was introduced to the market by a Turkish company by combining the words "suni (artificial)" and "tahta (wood)", is now integrated with the product in Turkish, surpassing the real definition of the product, "particle board".
How is Particle Board Produced?
The first stage in the production of particle board is to break the specially supplied trees into small pieces by crushing them in special crusher machines in order to provide the desired properties and to store the crushed trees in two separate classes according to the size of the chips. The top and bottom layer chips are dried together to the desired moisture content. Then, the sawdust pieces, which are divided into 2 separate classes, are mixed with special adhesives and hardening chemicals that will enable them to stick to each other. A separate special adhesive and additional chemicals are used for each class. The mixture of 2 different grades with added chemicals is dried with hot air to the desired moisture content. A separate humidity value is provided for each class. First, the mixture of very fine wood chips is laid on the bottom. Then the mixture with the larger pieces of sawdust is laid on top. Finally, the mixture of very small pieces of sawdust laid on the bottom is placed on top, again depending on the characteristics of the desired product. Afterwards, the board, whose rough outlines are given by the first pressing process, is subjected to the appropriate time under appropriate temperature and pressure in the second pressing process, ensuring that the fibers adhere well to each other. At the last stage, the boards are left to cool down in order for the structure to be fully formed. Following the completion of the specified cooling time, they are sanded to have the desired thickness and a smooth surface and made ready for final use.
Where is Particle Board Used?
With its durability and physical properties, particle board is delivered to the end user either in its raw form or after being subjected to various surface treatments.
Although they have various thicknesses and densities depending on the area of use, they are produced in thicknesses ranging from 6 mm to 40 mm and with a density of 500-700 kg/m3. Depending on the place of use, it can be produced with dimensions and width between 1830 mm and 2200 mm and height between 2440 mm and 4200 mm.
Particle board is suitable for use in almost every field and its usage area is quite wide. It is a product frequently preferred for kitchen cabinet bodies and doors, bathroom cabinets, living rooms, bedrooms and all other living spaces.
Today, the word chipboard has become integrated with the product, surpassing particle board, which is the real definition of the product.